Cost of steam plays a vital role for controlling productivity of the plant. First and foremost thing any process plant (small or big) owner should do is to get energy audit done for their boiler.
General feeling amongst by & large industries is that BOILER STEAM AUDIT is for only POWER BOILERS or big Boilers. But we strongly feel that Energy audit gives clear picture of losses in the plant. It’s like your account audit for the firm , trial balance gives you an idea to control the expenditure. Similarly Energy audit shall give you areas of energy losses the plant.
Before, we talk more about Energy audit, let’s check points heat recoveries.
There are 2 ways of going about it.
1) Macro level: installing Energy Savers. I.e. Energy saving equipment.
First check whether you have:
a. Economisers.
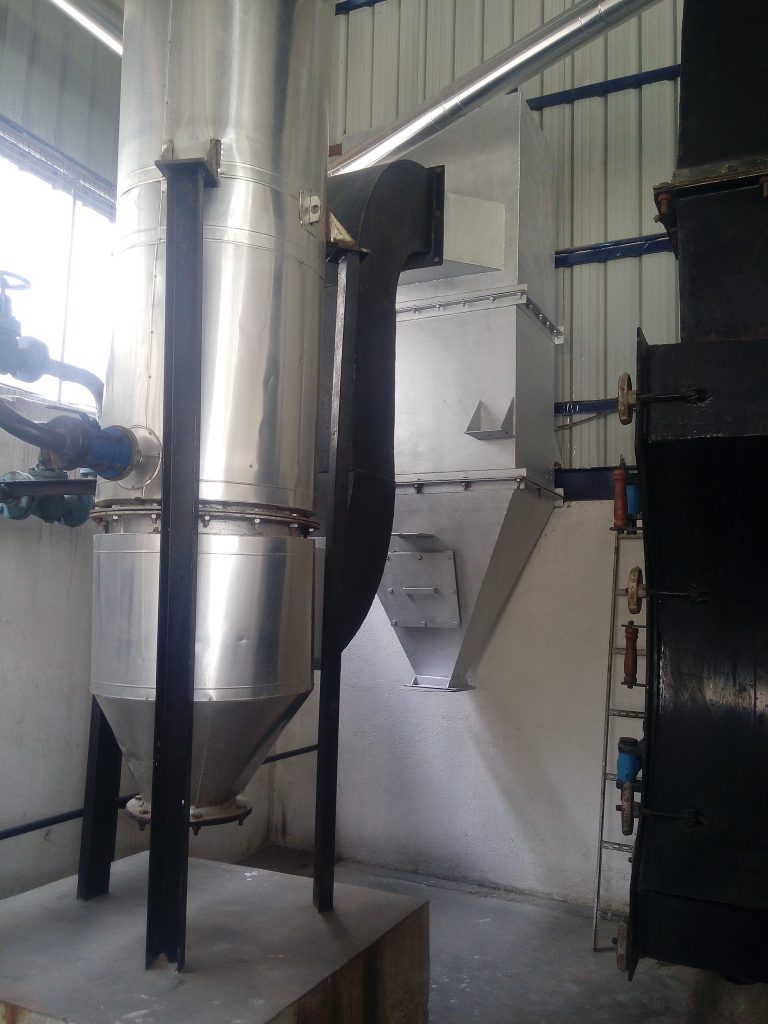
This is an equipment which extracts heat from exhaust flue gases and heats the feed water required for Boiler.
For energy conservation (to economise the production cost) The heat of the exhaust flue gas is utilized to heat boiler feed water temperature. It’s gas to liquid heat exchanger , critically designed to give optimum out put.
It gives 4 to 5% extra steam generation,
Note: This extra steam generation at no extra fuel consumption
b. Accumulators( for fluctuating load )
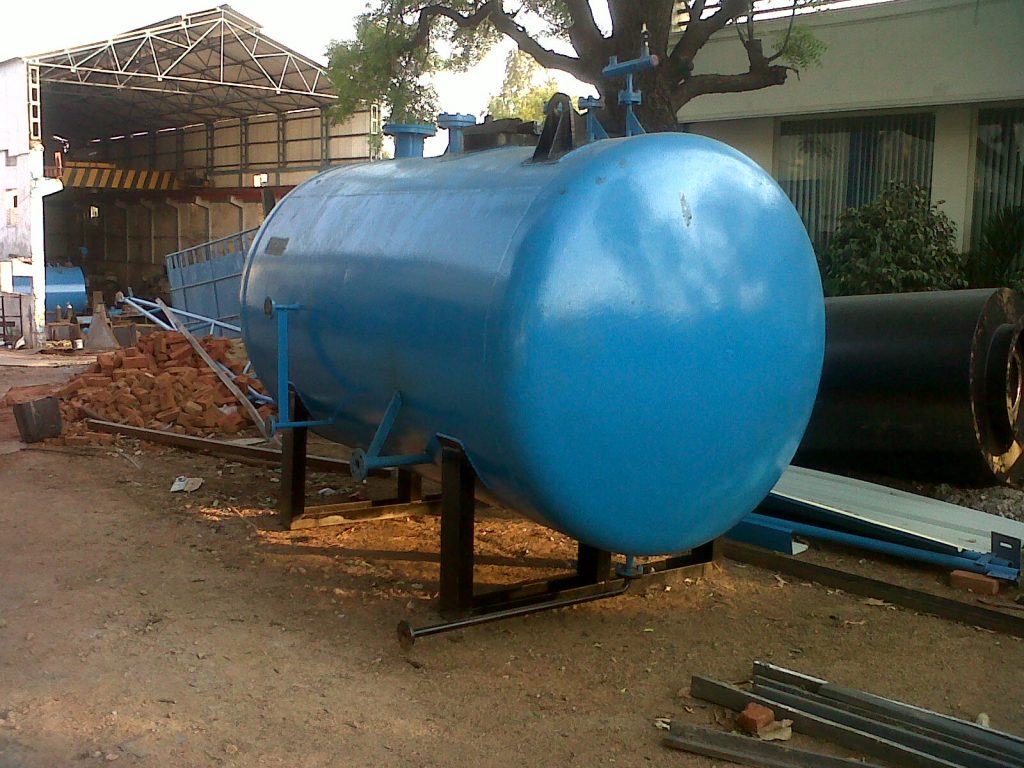
A steam accumulator is an insulated steel pressure tank containing hot water and steam under pressure. It is a type of energy storage device. It can be used to smooth out peaks and troughs in demand for steam.
In process plant it helps balancing fluctuating load. Gives steady steam for making quality products.
c. Air pre heater
This equipment is a heat exchanger that takes heat from the exhaust flue gases imparts it to cold air being fed to boiler for combustion , which in turn helps boost efficiency of boiler.
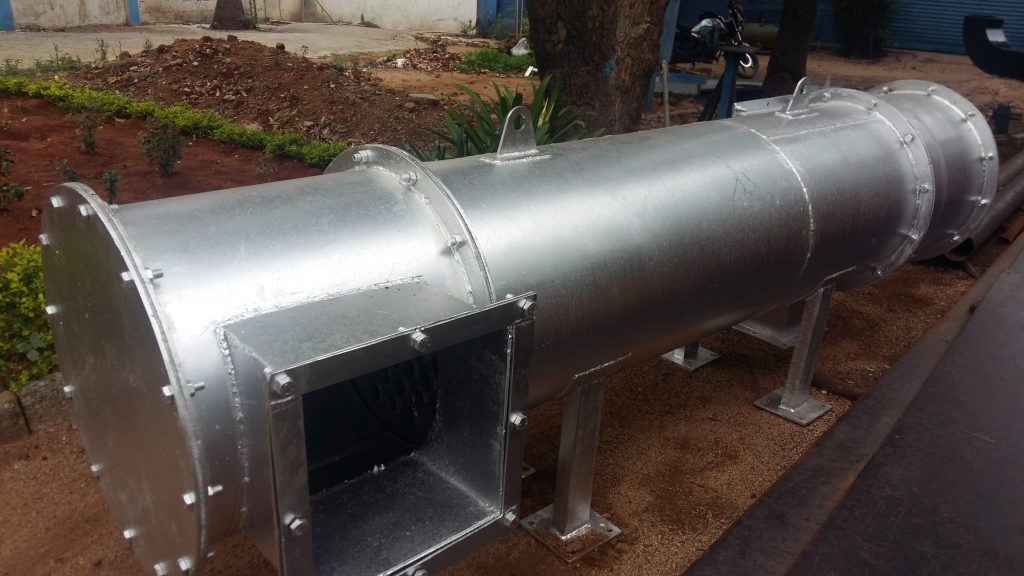
d. Blowers:
Induced & forced draft fan improves combustion efficiency of fuel. ( capacity of fans depends on load, that is required rate of loading of fuel type of fuel., Quantity of fuel to be burnt.
Blower has a very important role to get the optimum combustion efficiency and improve over all productivity. Often it is found that suitable balance is not provided. , Just to cut down the Boiler price.This will result in huge unburnt fuel in Boiler and inadequate supply of steam, in turn increases cost of steam per tonne.. besides frequent failure of fire bars due over heating.Do not ever compromise blowers.It also consumes more power, hence more power bill. Induced & forced draft fan ( as per combustion load that is required rate of loading of fuel and type of fuel.
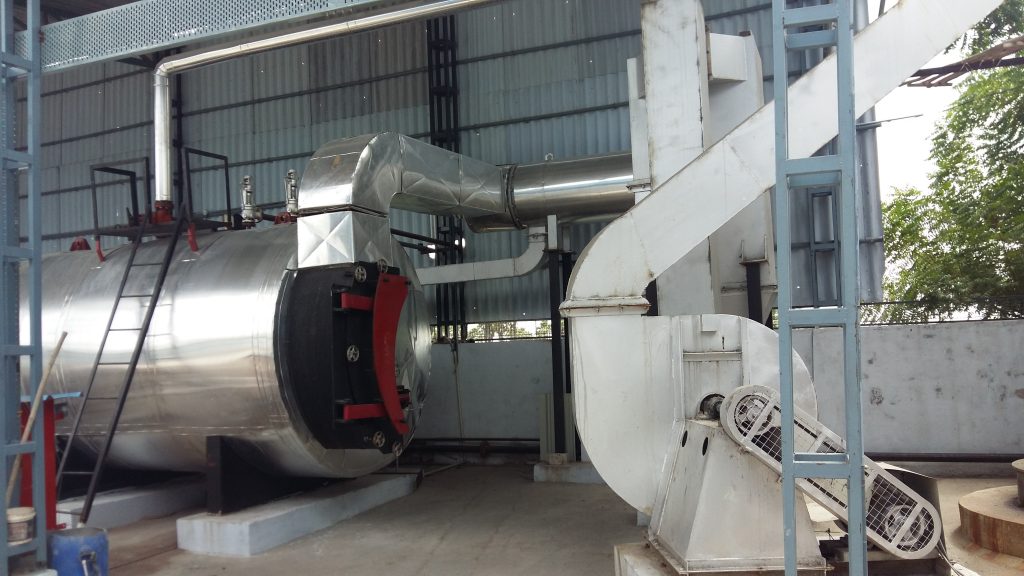
e. Super heaters.
2. Micro control system to enhance efficiency and productivity.
a. Automatic Blow down. It helps you save up to 1.5 to 2 % Reduces pay back period of the device and the boiler.
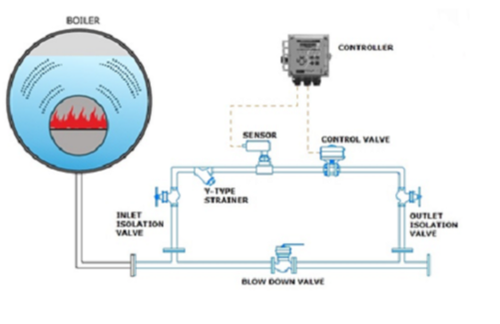
b. Mobary level controller: is an automatic water level controller , which operates automatically in response to demand and stops pump at no load or low load. It can cut your power bill by about 10 to 15 % when boiler feeding is done manually. There are also chances frequent failures of motor of the pump in the. Production loss.
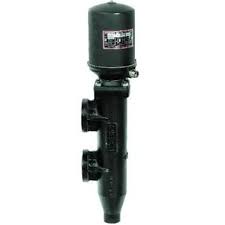
c. Condensate modules. Is simple fabricated module ( to designed condensate load ) to recover excess heat from the plant for recycling . Often people provide less no of this modules to save cost.
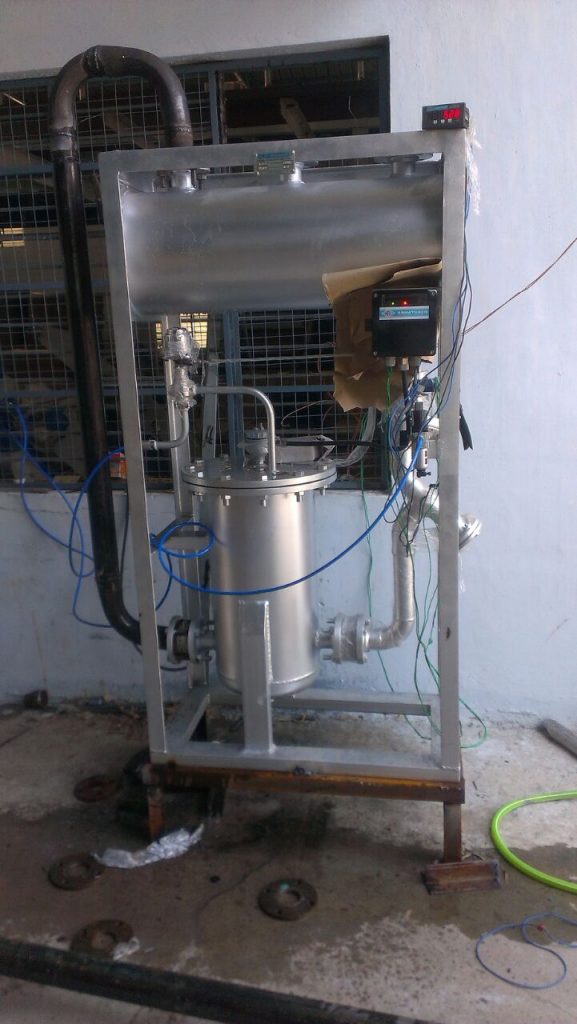
But they loose more. It’s like penny wise pound foolish.
d. Flash vessel: to collect excess steam from the condensate. This flash steam can be further utilized to save about 1 to 2 % of the steam.
e. Pressure Reducing stations.: It consists of (HP) high pressure & Low pressure LP side . This PRS has to be critically designed and fabricated as per process parameters, but often it is ignored just to make it cheaper. This ma result to loss equivalent to almost 10 to 15 % besides risk of safety. and getting bad quality of product.
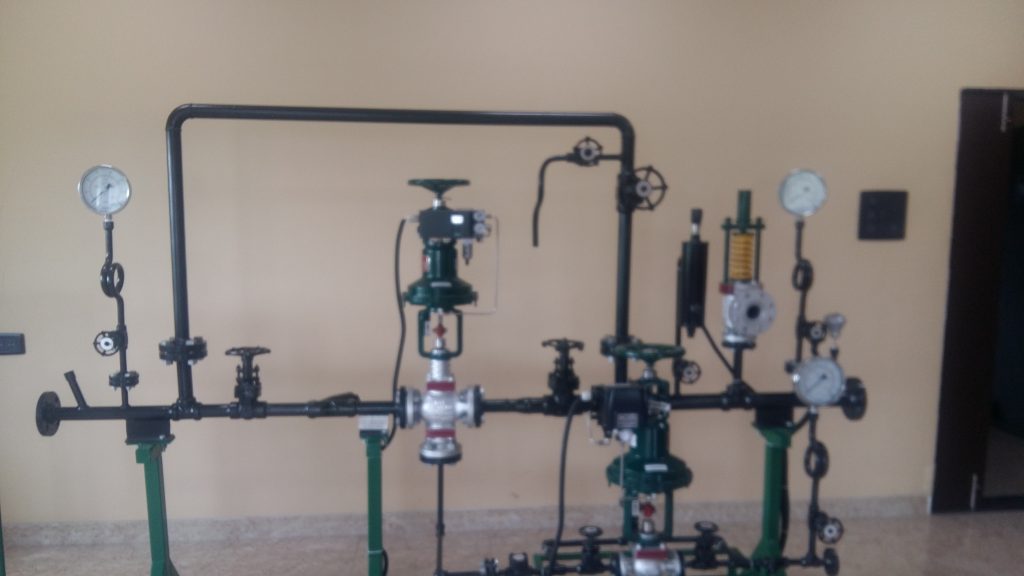
f. Steam Trap : Proper and efficient steam traping is must for achieving operational efficiency of steam generation. Many times Boiler users are casual about steam traps and ignore to repair or replace there steam traps in spite continuous steam leakages. With technology advancement there are very efficient thermo static steam traps available which can save upto 80 kgs of live steam per trap per hour . Just imagine the if the line is running into 50 to 100 meters , installing proper steam traps and maintaining them results in huge saving in the life span of the Boiler.
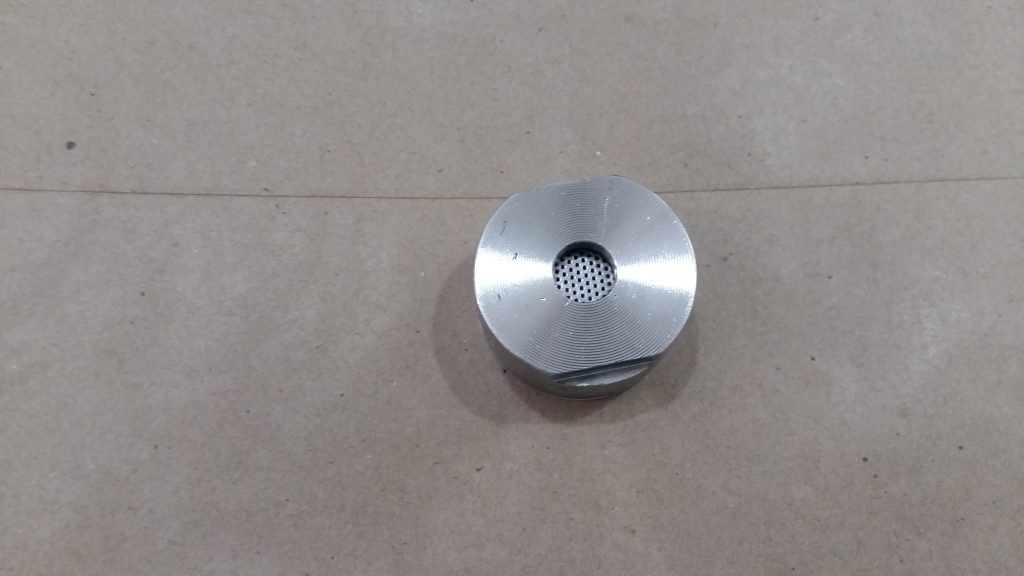
Energy saved is energy produced. Hope our energy conservation tips helps you in improving energy efficiency of your unit. Kindly send us your queries on [email protected]. For free consultation of energy efficiency of your organization kindly call us on 9490494915